Featured Golf News
A Tour of the Titleist Factory
A Titleist NXT S golf ball sits before my eyes. I pick it up, spin it around in my hand and search for the tiniest imperfection: perhaps a slight blemish in the Surlyn cover or maybe the printed logo isn't quite right. I could inspect it further by comparing this ball against others from the same sleeve to learn if there are any differences that might affect ball flight or distance, and I'm guessing it's highly unlikely I will detect any issues.
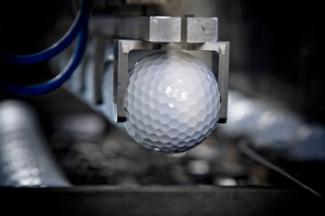
Titleist Custom Selects
Now I know why each ball is identical to the next, and that no matter how many Titleist balls I shank into the water or lose in the woods, the next one I pull from my bag will be indistinguishable from the one I just lost. I've just come from a tour of Titleist Ball Plant II, where nearly 1 million balls come off the assembly line on a daily basis, from the DT SoLo to the NXT Tour to the new orange-numbered Velocity.
It is, to say the least, an elaborate operation that runs 24/7, involving approximately 400 workers, intricate machinery and state-of-the-art technology that results in the simultaneous production of golf balls with various dimple patterns, cores and covers. Located in North Dartmouth, Mass., about an hour drive from Boston, the Acushnet Company manufactures such products as Titleist and FootJoy and operates three ball plants that employ more than 1,000. The Titleist line of Surlyn-covered balls is made for worldwide distribution at Ball Plant II.

Core Prep Jig
This is where it all starts. We know where it often ends - with a millionaire holding up a shiny trophy. There were 33 PGA Tour winners last season that played Titleist golf balls. Titleist is such an iconic brand it was once used in a "Seinfeld" episode. George Costanza, pretending to be a marine biologist, rescued a suffocating whale that had a golf ball lodged in its blowhole as a result of Kramer hitting shots into the ocean.
"Is that a Titleist?" Kramer asked sheepishly when George produces the offending item.
So when I was given the opportunity to visit the facility and perhaps learn the secret to their success I readily accepted. It didn't take long to realize that the process of making a golf ball involves a comprehensive system of checks and balances to ensure consistency with every ball that heads to market.
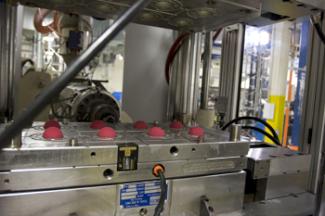
Casing Injection Molding
As I walked past the whirring machines and watched balls rolling through tubes and being deposited into bins, it was immediately obvious that no stone is left unturned. Inspections are conducted during every step, from the mixing and heating of the virgin plastic polymer that will eventually produce the cover, to the sizing, molding and cooling of the rubber core, to the final painting of the ball, to the stamping on of the logo.
Thanks to modern technology, much of this can now be accomplished with computers, UV-light and electronic-vision sensors. But when major flaws are detected, balls still undergo inspections by hand. At the final stage in the process workers examine balls that are randomly selected, searching for the slightest imperfections. Merely a slightly lighter imprint on the "T" in the Titleist logo is cause to reject the ball, even though such a flaw would not affect performance.
The first step in making a golf ball is in the mixing and curing of the core material, with the recipe depending on whether the cover is designed for a softer feel, greater distance or increased spin. The material is then deposited into bins that are labeled for the various balls in the Titleist line. Although Titleist makes 24 different balls, only 10 on average are produced on a daily basis. Production schedules are based on demand.
The material for the core begins as a slab of rubber that is fed into something resembling a pasta machine, where it is heated, pressed and rolled. The resulting long sheet is then placed on shelves and left to cool for two hours before being mechanically sliced into long, thin strips. The strips are cut into smaller pieces, which are placed into a mold that shapes the core.
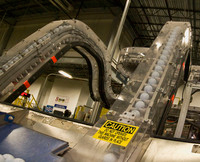
Packaging Process
The cover is attached to the core in two pieces that look like halves of a broken eggshell. The top half is placed onto the core, followed by the lower half and then the two halves are spot-welded together to prepare for the cover molding step. In this compression molding step, the cores, jacketed by the two cover half-shells, are placed in molds and formed under heat and pressure. The mold is made up of two plates, each containing hemispherical cups. Each cup contains the particular golf ball’s dimple pattern. The ball is buffed so that the ridge created by the molding of the halves disappears.
Throughout the process, balls are flowing down an assembly line and dropping into bins. After the logo and numbering are stamped on, a latex primer and finishing coat are applied by placing the balls on top of a rubber tee-like holder, where they are spun and painted by two spray guns.
And with that, a gleaming new Titleist emerges. It's all rather complex. But after watching the process from raw materials to finished product, it was easy to understand why each Titleist is precisely like the last, and no matter how many I lose, there will always be another coming off the assembly line ready to be teed up.
Rob Duca is an award-winning sports columnist who wrote for the Cape Cod Times for 25 years, covering golf, the Boston Red Sox, the Boston Celtics and the Boston Bruins. He is now managing editor of Golf & Leisure Cape Cod magazine and has written for a variety of other publications, including Sports Illustrated, the Boston Globe, Yankee magazine and Cape Cod Life.
Story Options
![]() |
Print this Story |